Advancements in technology are revolutionising mining operations, enabling businesses to analyse large datasets quickly and effectively. The result is more accurate geologic modelling which in turn helps mines operate more efficiently and with less risk.
By Fiona Jeffreys
The leading cause of pit wall failures in mines is unrecognised or incorrectly modelled faults. However, innovative subsurface technologies are enabling mining companies to quickly analyse large geological datasets, helping to create accurate structural models and identify and characterise structural features such as faults and fractures.
Visualising these features in 3D ensures geotechnical engineers and resource geologists can understand the underground to maximise resource extraction while ensuring safe pit wall designs and improving mine safety and efficiency.
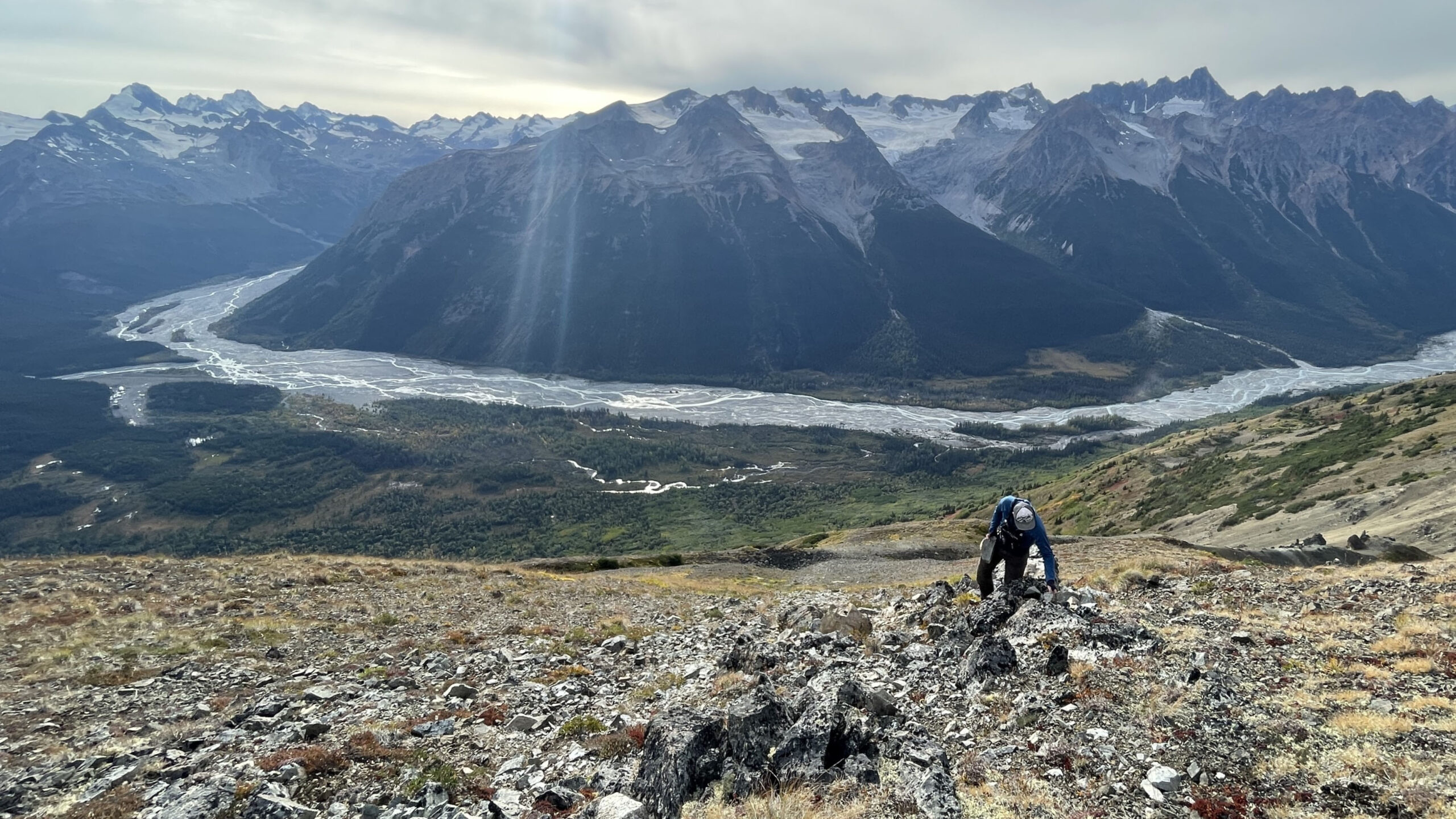
Structural geologic field work in remote northwestern British Columbia in Canada.
Credit: Teck Resources
“Accurate structural models are imperative in mining, providing critical insights for geological and geotechnical models, that can inform pit slope stability and resource extraction optimisation,” said Neil Seifert, Senior Project Technical Specialist at Teck Resources Limited.
Teck Resources Limited is a leading Canadian mining company with a focus on responsibly providing the metals essential for global development and the energy transition.
Optimising resource extraction
Seifert is part of the Orebody Knowledge (OBK) team, a group within the Technical and Planning department. He and the team are responsible for providing technical expertise to the operations, advanced projects, and exploration initiatives.
“Our work in OBK has two focuses: technical subject matter expert (SME) support and applied OBK innovation to drive value generation and risk mitigation. The technical SME side involves creating detailed 3D structural models for various projects and is critical for understanding the geological features of mining sites,” he said.
Identifying and characterising structural features such as bedding, jointing, faults, fractures etc., helps ensure the safety and efficiency of mining operations. Accurate modelling of these features in 3D ensures geotechnical engineers and resource geologists can maximise resource extraction while ensuring safe pit wall designs.
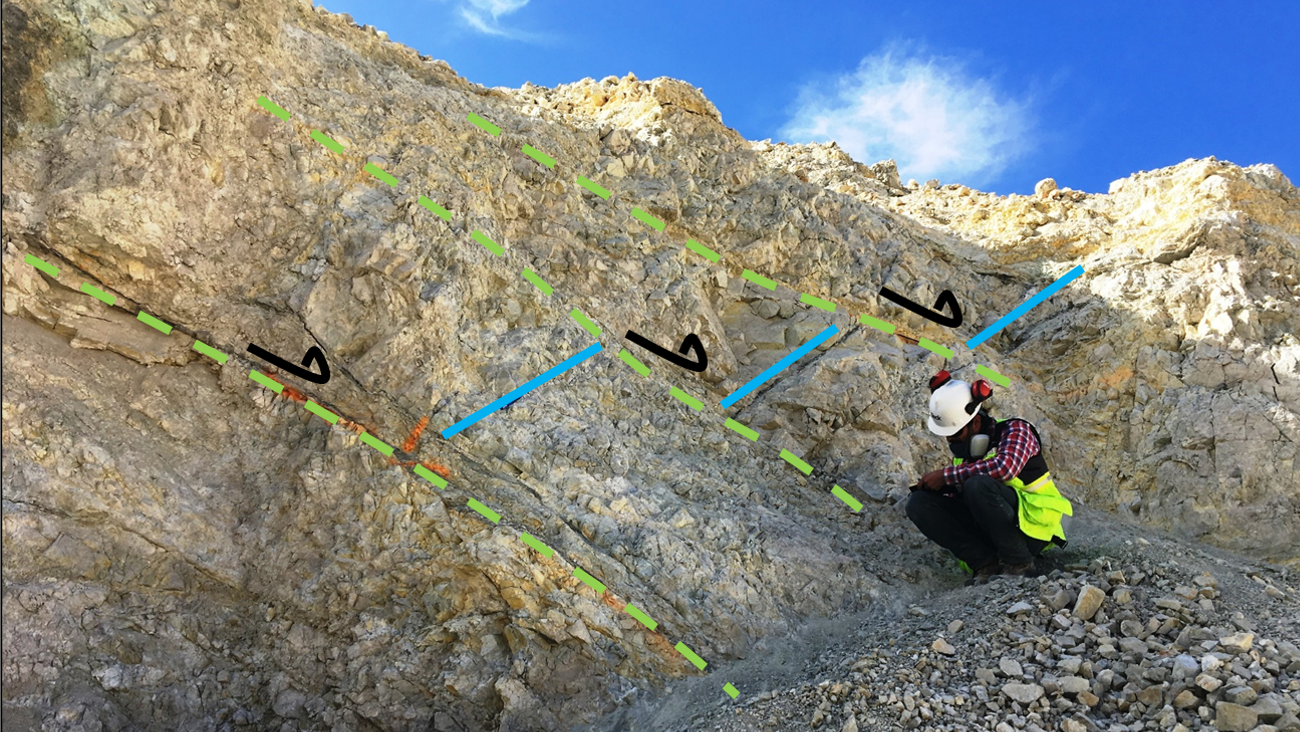
Faults indicated by green strippled lines, offset contact in blue and (arrows) showing the direction of movement
Credit: Teck Resources
“An unrecognised or poorly characterised fault with an unfavorable angle to a pit wall can cause pit wall failure, resulting in significant safety risks, can amount to enormous costs to operations, and can make ore inaccessible for future mining” Seifert said.
Robust structural models require the incorporation of multiple data sources, such as oriented drillhole measurements, televiewer, geomechanical, geological, and structural core logging, hydrogeological, geophysical, and geochemistry datasets, as well as field and pit wall mapping.
“Seequent’s Leapfrog Geo has enabled our team to integrate diverse datasets and create robust 3D models that visualise the subsurface to more accurately pinpoint geological features,” he said.
Overcoming structural modelling challenges
Seifert and the team have been working on making structural modelling more accurate and efficient while allowing models to be easily incorporated into downstream workflows such as geotechnical design and resource estimation.
“One of the significant challenges in structural modelling is creating a single fault surface based on multiple datasets with varying degrees of accuracy. We need to be able to communicate the accuracy, confidence, and uncertainty in our models to downstream stakeholders,” said Seifert.
”“Leapfrog Geo has tools that help to overcome those challenges allowing the integration and interpretation of multiple sets of data to create accurate and scalable models. We also use Leapfrog Geo to create confidence heat maps of faults showing locations of confidence along a fault plane” he said.
Another complex challenge for the team is creating nested models, a smaller-scale bench level model that is dynamically linked to a larger-scale regional model, requiring advanced software to maintain dynamic links between scales.
Cloud-based Seequent Central helps facilitate this by providing shared 3D visualisation, team collaboration, and tracking of geological data in one auditable environment. It allows independent work on smaller models that integrate with the master model, promoting a collaborative approach.
“Seequent Central allows us to work independently on smaller, bench-scale models, while integrating back into the master model, fostering an integrated and collaborative approach to our modelling,” Seifert said.
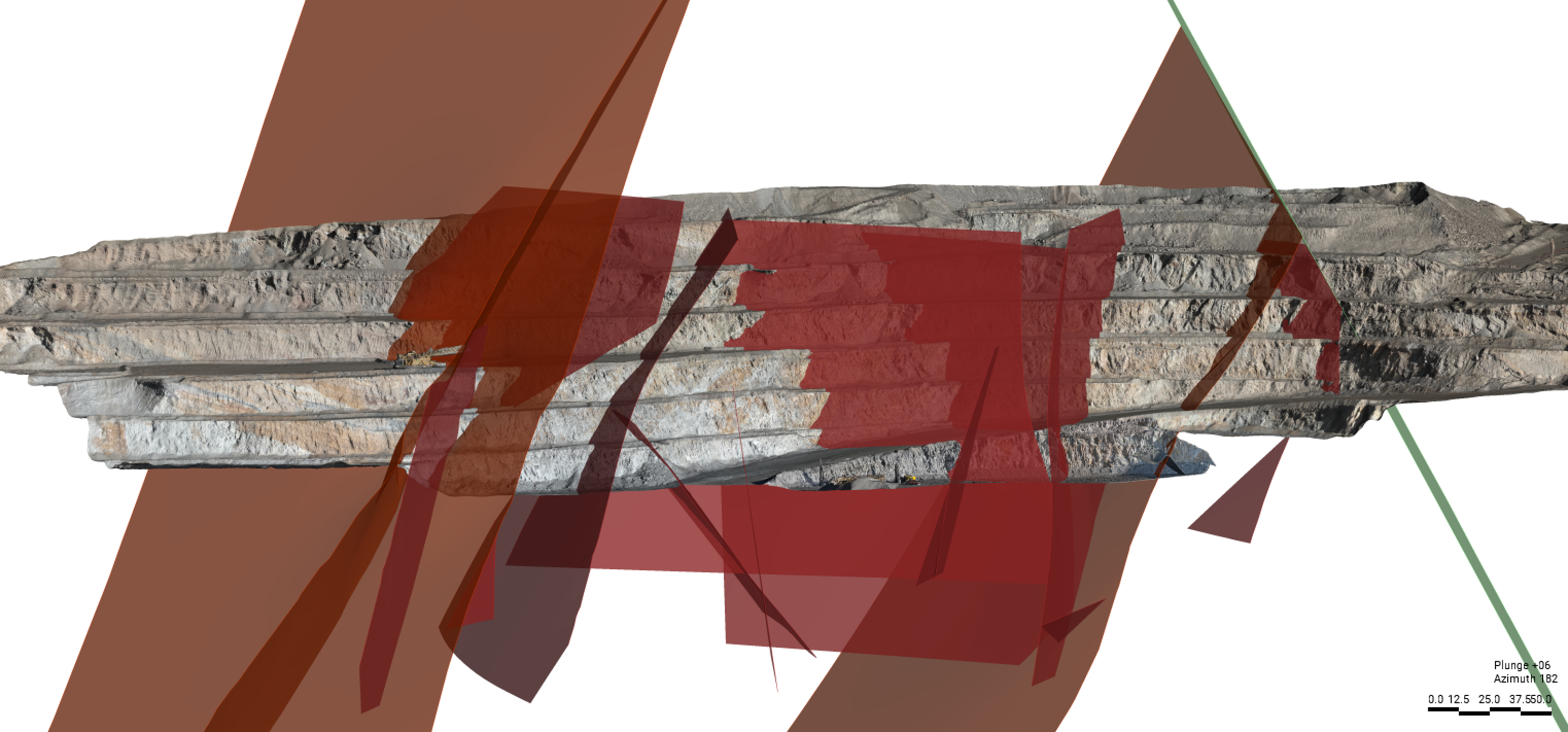
A 3D mine model of a complex fault system shown in red overlain on photogrammetry
Credit: Teck Resources
Flexing machine learning muscles
Innovation is at the heart of the work Seifert and the OBK team do. They collaborate with external consultants and service providers to develop new workflows and leverage geoscience data in novel ways.
Integrating multiple data sources, particularly legacy data, comes with its own set of challenges. Structural data is often inconsistently collected between various historical campaigns making integration and interpretation difficult.
Seifert and the team have taken advantage of recent advances in machine learning to tackle these challenges. For example, they are developing technology to gain new structural geologic value from historical core imagery by scanning an entire core database and utilising machine learning to detect faults, fractures, and their orientations relative to the drill core automatically.
They are also working on optimising present-day core logging by developing machine-learning algorithms to automate the classification and interpretation of televiewer data, which scans boreholes to detect structural features.
“As the industry continues to evolve, integrating cutting-edge technology with expert knowledge will remain key to our success. Ongoing investment in technology and expertise will be crucial to help achieve our global sustainability goals and address the increasing demand for critical minerals,” Seifert said.
- Canadian mining companies recorded over $68 billion of impairments (reduction in the value of a company’s assets) from 2003 to 2016
- Roughly 30% of impairments resulted from technical error – inadequately predicting the physical rock and mineral properties of a project
- 35% of technical errors are attributed to ore access which are directly linked to geotechnical issues (pit slope failures, underground failures, unexpected water ingress)