They estimated it would require around 600 boreholes for the project, and EMerald Geomodelling reduced that by 30%. That’s around 200 less boreholes to do in the end. This contributed to the project saving up to six months in total, which was almost 50% of the projected time.
Where is the bedrock? Civil engineering companies invest major time to answer this important question because they risk overrunning their budgets if they get it wrong.
Now, airborne geophysical survey data is helping them reduce time, risks, and costs through accurate resistivity modelling, which can map the depth-to and overburden of the bedrock.
Previously, airborne surveys were mostly applied in mining exploration, using plane-based instruments to cover large areas for electromagnetic data. Today, civil projects are also reaping the benefits using agile helicopter-based instruments with higher resolution.
“What civil companies are often looking for is the depth to bedrock. You always need to know where the bedrock is to ensure stability. Also, if there’s groundwater involved, it can affect the hazard risk for rock and landslides,” explains Toke Søltoft, director and geophysicist at Aarhus GeoSoftware (part of Seequent).
The data is more accurate when the survey can follow the landscape. Better data coupled with the development of higher resolution transient electromagnetic (TEM) instruments means infrastructure projects can reduce ground condition risks – and costs.
“In most geological settings, the resistivity models that you get from airborne EM give you a good indication of where the bedrock interface is,” says Andi A. Pfaffhuber, CEO and co-founder of EMerald Geomodelling.
Andi completed a PhD in geophysics before diving into geotechnical engineering at the Norwegian Geotechnical Institute. He saw firsthand the challenges of both fields. After 12 years in these fields, he co-founded his company with a vision of uniting geophysics, geology, and geotechnical data using machine learning to build better models.
Their results speak for themselves. EMerald Geomodelling used airborne survey data, Workbench modelling software, and machine learning to help one Norwegian highway project decrease drilling costs by 30% and time by up to six months (50%).
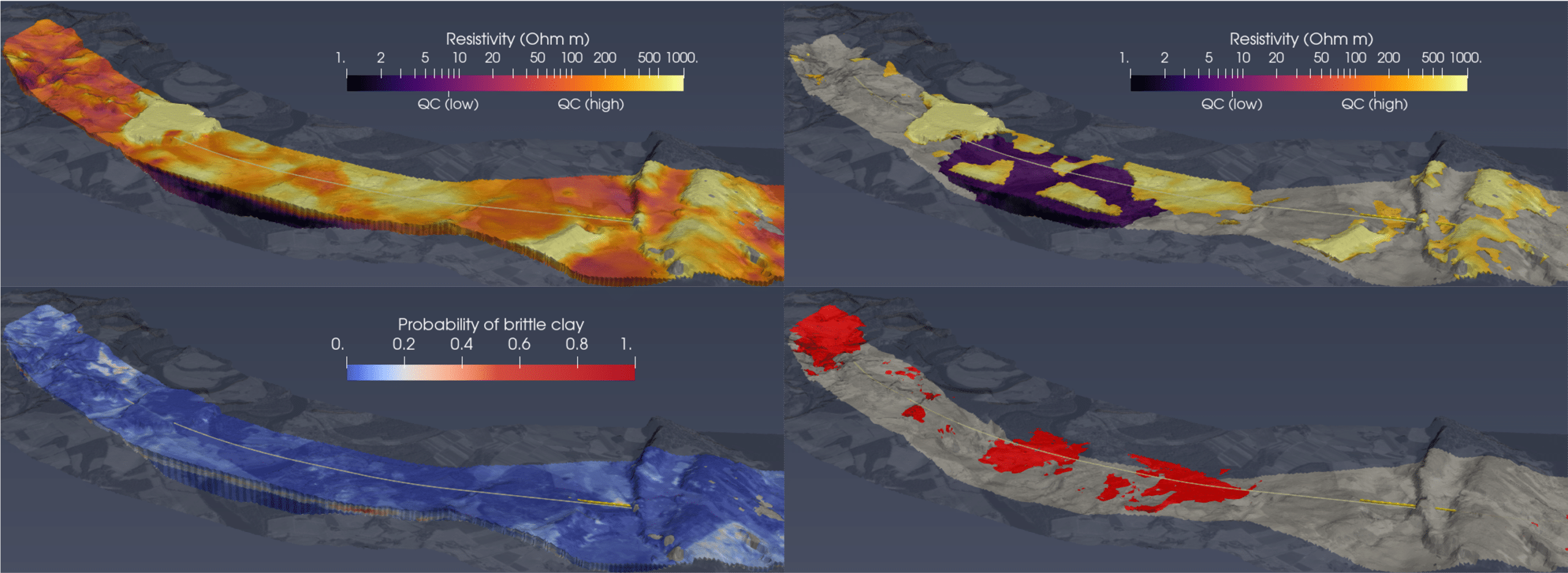
Top left: 3D volumetric grid of electrical resistivity (sediments only; material below bedrock clipped). Top right: quick clay can be ruled out based on resistivity alone where it is very high or very low. Bottom left: Computed probability of weak, sensitive clays are expected based on geophysical and geotechnical data. Bottom right: Extracted volumes where weak, sensitive clays are expected. (Image credit: EMerald Geomodelling)
The Norway E6 project
Norway is known for its glacial fjords, coastlines, and vast landscapes. While beautiful, below ground it’s complicated.
Amidst challenging ground conditions, including glacial deposits and complex marine clays, Andi’s team needed to help find the best route for a 19-kilometer highway.
Uniquely, the project area contained segments with extremely variable sediment thickness and properties. It would have required hundreds of boreholes to gain the necessary insights to find the ideal alignment. Thus, the project owner was open to out of the box thinking.
“There was a lot of heterogeneity and therefore an even higher need for full spatial coverage of the data they could base their decision on. Time and the speed was essential,” says Andi.
A geotechnical team had estimated it would require 600 boreholes to determine the best route, but decided to use airborne surveys to help target drilling locations.
“That’s the big value proposition for most geophysical methods, that you can fill in the gaps between boreholes, that you can get a more complete picture, more complete view, in a more efficient way,” Andi explains.
TEM data from the airborne survey was used to find areas where the bedrock depth varied so that drilling could be constrained to those areas – meaning less boreholes were needed in total, cutting down those costs.
“If you take an airborne survey over a huge area and then interpret it using existing knowledge from drilling, you can create models where you can understand the uncertainty,” explains Toke.
“Then you can do more drilling in the areas where uncertainty is highest.”
Does survey data reflect reality?
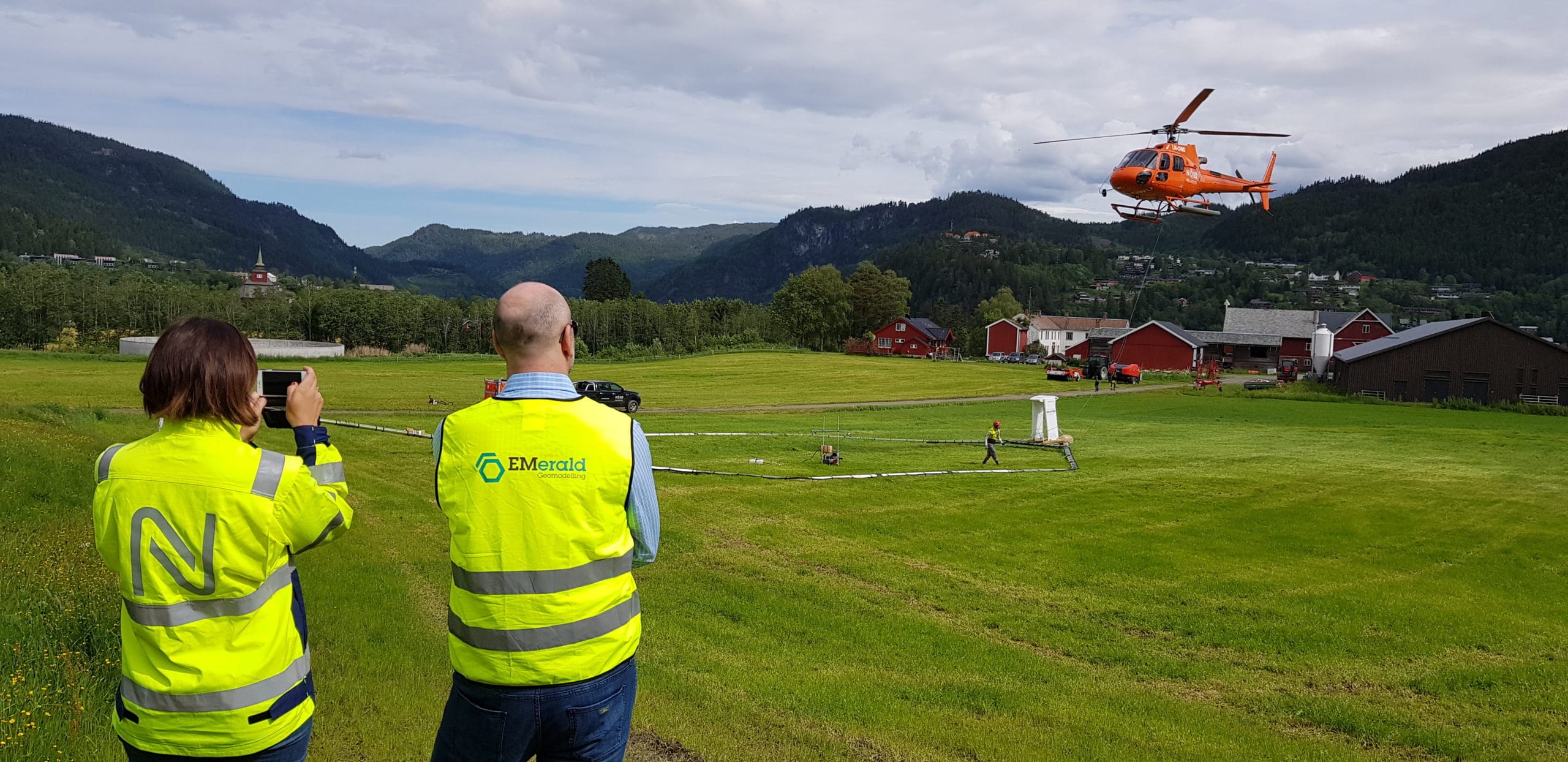
The EMerald GeoModelling team gets ready to launch an airborne TEM survey. (Photo credit: EMerald GeoModelling)
The team’s 170-kilometer airborne TEM survey took just two days, much faster and providing greater resolution in complex areas than ground-based techniques.
“I could plug in the SkyTEM survey data straight into Workbench and get first versions out really quickly: Get some first models, use our algorithms on them, and have a first bedrock topography fast,” says Andi.
This quickly gave the project team a clearer understanding of the underlying geology, allowing them to plan for additional data collection and to begin planning the best route.
“Workbench has the instrument information: the geometry, wave form, as well as the time gates, current and past specifications for how the instrument works,” explains Toke.
“Having these correct specifications is extremely important to get the most accurate resistivity models from the survey data.”
Each instrument is unique. Emerald Geomodelling uses SkyTEM systems for these airborne surveys in Norway. Both SkyTEM and Aarhus GeoSoftware had their start at Aarhus University in Demark.
“The fact that we use mostly SkyTEM as the geophysical system in our projects is a key driving factor of why we also use Workbench because those two have been very much developed together,” says Andi.
“There is definitely no other geophysical software package that is better suited to process and invert SkyTEM data.”
Models are only as good as the data within them. Workbench allowed the team to quality control the models made from the data and account for misfitted models and reprocessing of data.
With clean data in hand, they were able to run inversions on the data to explore the subsurface in 2D profiles and 3D grids and volumes.
“There are quality checks you can do to see how big the misfit is between the models compared to the data. You often re-process and rerun a new inversion again, until you have models that fit the data and you’re happy with the results,” says Toke.
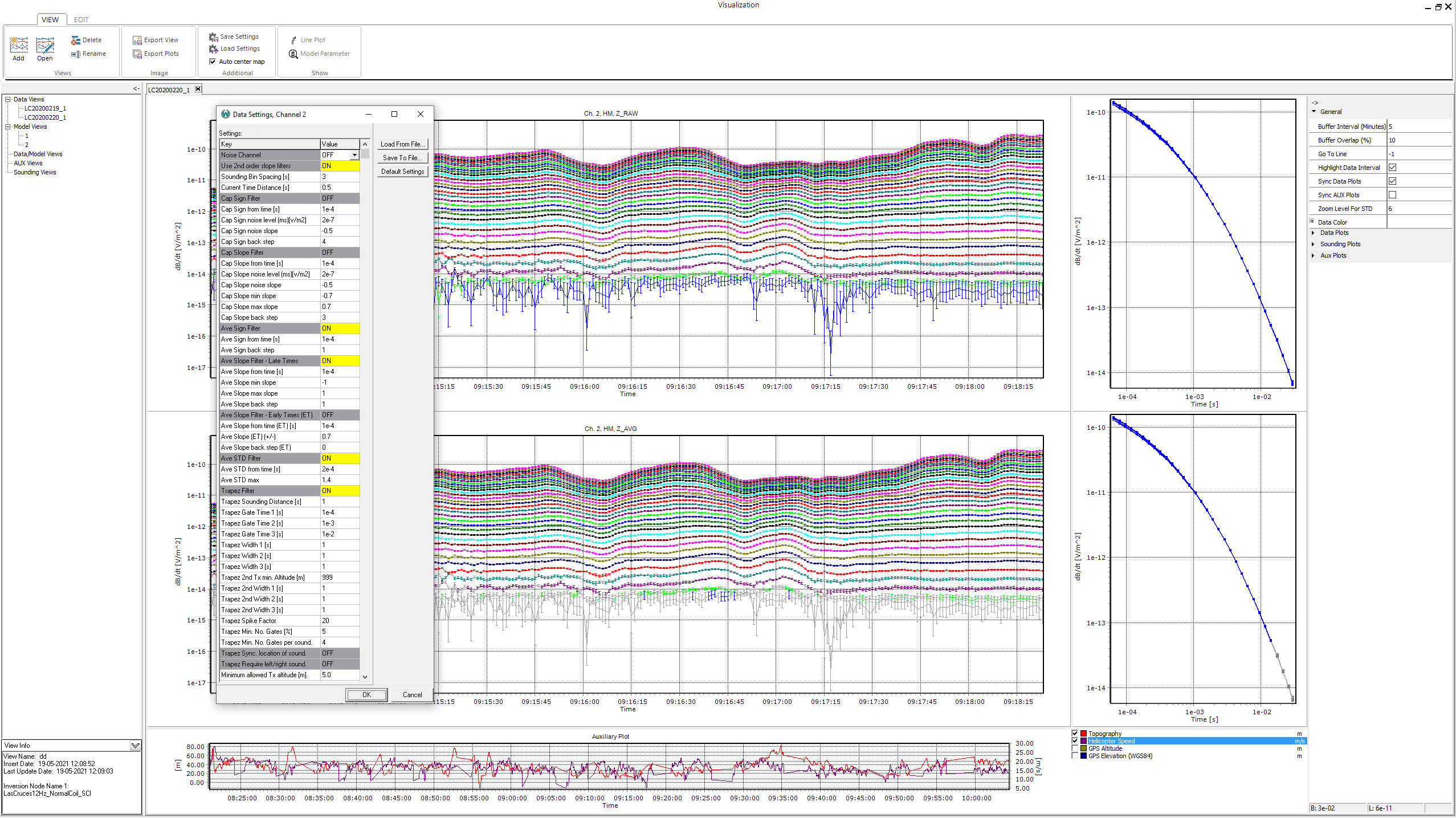
Setting processing filters to remove noise in data.
Clean data for machine learning
Some initial borehole information already existed for the project. The project team put the Workbench resistivity models and the borehole data into Emerald Geomodelling’s neural network for modelling.
“Workbench is the first step in our workflow. And then we bring in the other data and we use our various machine learning algorithms to develop 3D models,” says Andi.
The machine learning program was able to rapidly model patterns and make connections, producing a bedrock model that took all information into account.
Using this comprehensive bedrock model, the team could more accurately target future drilling to areas where the uncertainty was highest – and reduce it by drilling there. The more boreholes that were done, the smaller the final uncertainty in the integrated model
More importantly, they could avoid unnecessary drilling in areas where they had higher certainty about ground conditions – saving time, reducing costs, all while minimising geological risk.
“By putting the resistivity models into this neural network, you can go in and say confidently ‘This area is where the bedrock is, this is how much overburden there is, and in these areas, we need to do more investigation,’” says Andi.
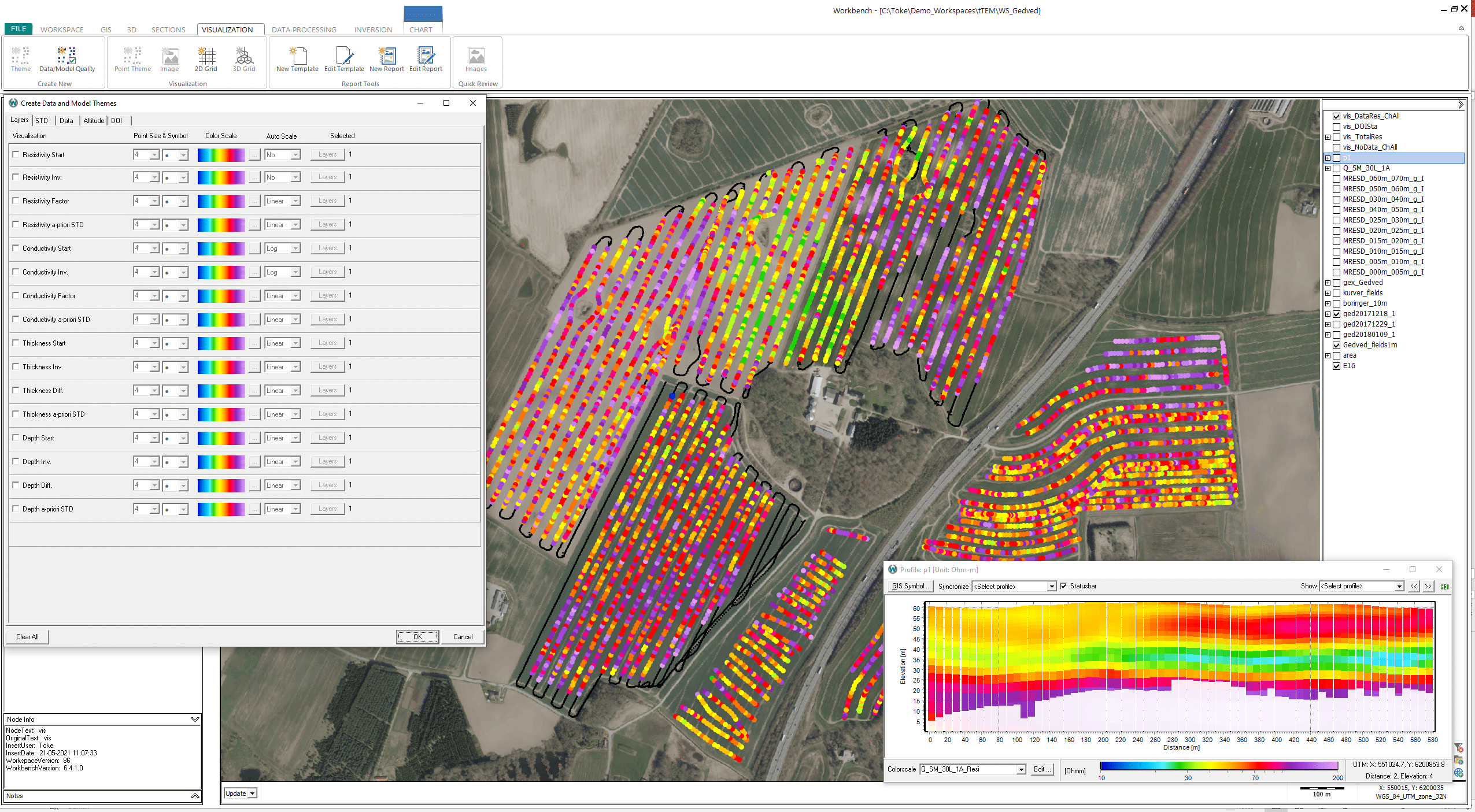
QC tool to display inversion parameters and model fit.
Quick quality checks for borehole data
Previously in civil projects, people would do a lot of drilling and trust that the borehole information was accurate.
“But it always depends on who took the samples, how well it is described, and other factors,” explains Toke.
Thus, despite exhaustive drilling, geological risks often led to budget overrun because of the variability between boreholes and from data entry and interpretation errors. Workbench resistivity modelling helps teams to reduce both.
“If you have borehole lithology as well as resistivity information from boreholes, they can both be imported into Workbench. The borehole resistivity information can be used to constrain the inversion of the resistivity models,” says Toke.
“This will result in resistivity models that fit both the borehole resistivity, borehole lithology, and the airborne TEM data as closely as possible.”
By bringing all data together to compare the models, Civil engineering companies can then review those boreholes that don’t match the data and try to account for the differences.
On the E6, Emerald Geomodelling brought their SkyTEM data into Workbench for modelling and then processed it using their machine learning algorithms alongside the borehole data.
The program could compare and analyse all available data to make a more accurate model. Also, if any new borehole or TEM data came in, Andi’s team could instantly update their model by simply plugging it into the algorithm again.
Their models were more accurate because they were based on the latest information, unlike the static models more common to geotechnical projects.
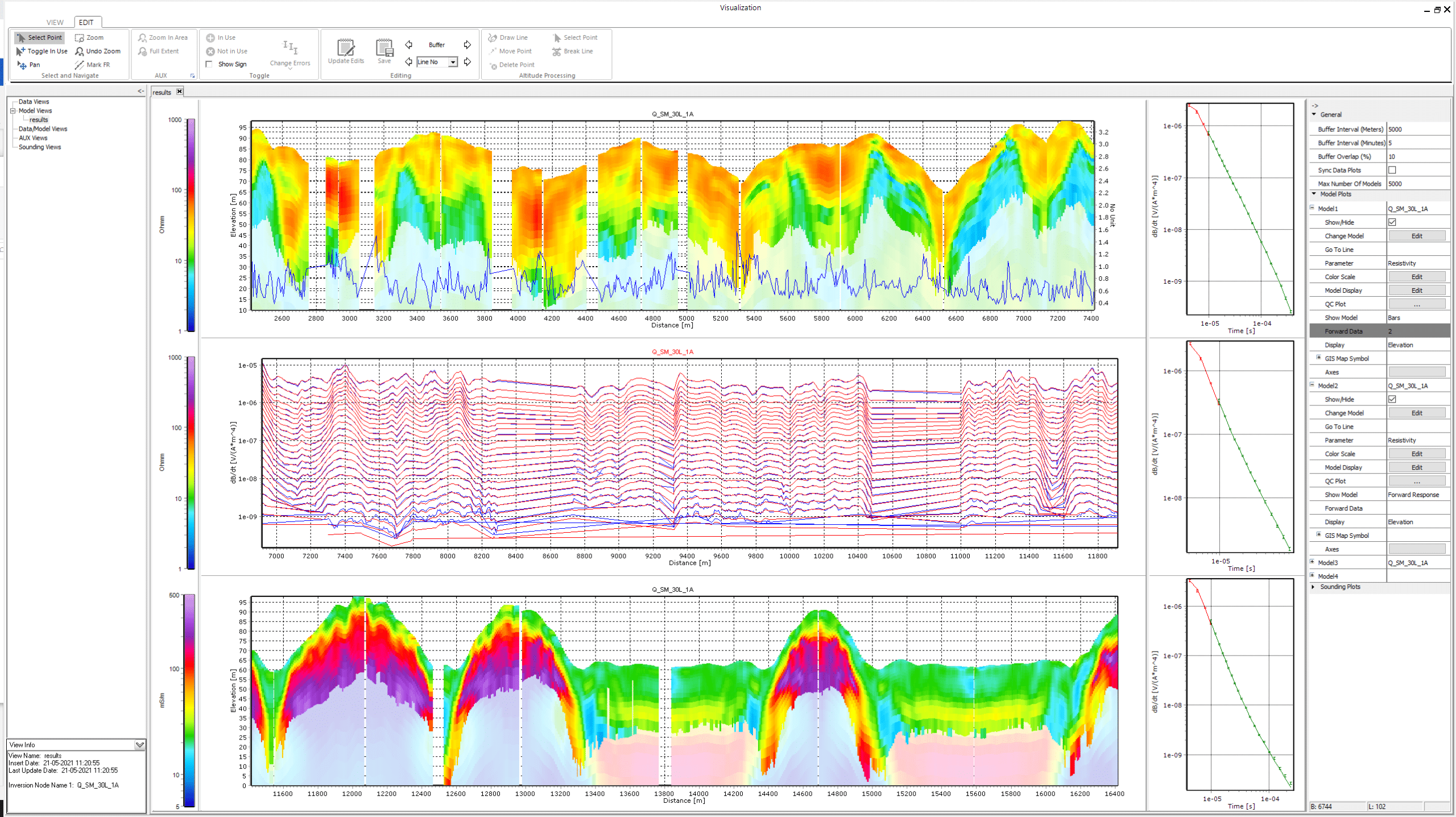
Final resistivity models
Saving costs and the environment
EMerald Geomodelling validated their approach when the E6 project got underway.
“The biggest value of the integrated model in this project was that a problematic area was evident just weeks after the survey and without a single borehole. The alignment was reconsidered and drilling was done at the really critical spots right from the start,” says Andi.
“During the months following the survey, while the targeted drilling was done, we frequently updated the model by re-running the machine learning algorithm and the engineers always had the most accurate and latest model to work with.”
Civil works projects like the E6 are often massive and have a big impact on an area. By exporting Workbench models into geological modelling or BIM software, not only are error, risk, and costs were minimised, but also the project’s footprint.
“Norway has a fair bit of really challenging geotechnical conditions. And is a very labor expensive country. Doing a lot of drilling costs a lot. So, saving on drilling is a big save here,” says Andi.
“Also, by doing less drilling and creating the road where it’s most feasible, you reduce emissions and environmental impact.”
As civil works projects involve more stakeholders and regulators, demonstrating reduced impacts is a win-win for the planet and for contractors.
Aarhus GeoSoftware (Workbench software) has joined Seequent, working together to build a better understanding of the Earth – see a copy of the recent announcement here: www.seequent.com/bentley-systems-announces-seequents-acquisition-of-aarhus-geosoftware