Given four of the world’s biggest economies are cities sitting along fault lines, protecting buildings against earthquakes, and especially making high-rise offices and homes resistant to seismic activity, is becoming increasingly critical. So, what are the techniques currently in use, and where is research and application going?
Base isolation
This technique effectively separates the substructure of a building from its superstructure. Most commonly it’s achieved by suspending a building on lead-rubber bearings. It is a solution that came to the mind of New Zealand seismic engineer William Robinson back in 1974 and is thought to sit beneath more than $100 billion worth of structures around the world.
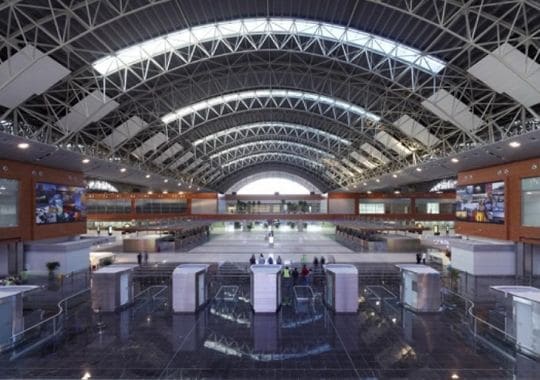
Some designers have been trying to take the base isolation concept even further. Japanese engineers have experimented with using huge compressors that can pump air between a home and its foundations within a second of receiving a warning from seismic sensors. They’ve been able to lift the superstructure by a couple of centimetres. It’s a solution that could be valuable for smaller structures, but it’s hard to see how it could be scaled up for larger buildings.
Base isolation is effective but expensive, so it’s often reserved for buildings that would be vital during an earthquake, such as hospitals or airports. For example, the Sabiha Gökçen International Airport in Turkey incorporated 300 isolators into its construction. Theoretically the 2 million square foot complex can withstand a quake of 8 on the Richter scale. And interestingly, Apple Park 2 in California recently became the largest base-isolated structure in the world.
Internal dampers
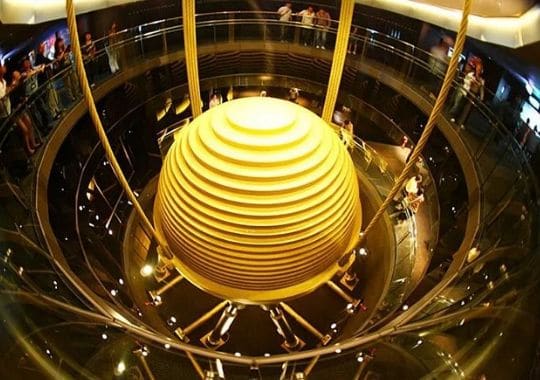
Taiwan’s 1,667ft tall Taipei 101 (until 2010 the world’s tallest building) uses a vast internal pendulum to counteract vibrations, either from earthquakes or high winds. The 730 – ton ball of steel hangs between the 87th and 92nd floors within a sling made of steel cables. The Shanghai Tower adopts the same concept but outdoes it with a 1,000-ton damper and throws in 980 piles, nearly 300ft deep, encased in more than 2 million cubic feet of concrete. In each instance these mass dampers are tuned to match the building’s natural vibrational frequency and help them absorb and cancel out seismic movement. A different take on the damper solution was developed for Japan’s Mori Tower, one of the tallest buildings in Tokyo. Nearly 200 shock absorbers are filled with thick oil – as the building moves, the oil shifts in its containers, in the opposite direction to the movement, helping to neutralise it.
The Earthquake Invisibility Cloak
This futuristic concept proposes avoiding the need for dampers or base isolators by ensuring the earthquake never reaches the building in the first place. It calls for enormous concentric rings of plastic to be set into the earth’s surface around structures to break up and divert the damaging waves that ripple towards them during seismic activity.
Resilient new materials
Engineers have been experimenting with special polymers and metal foams developed for the aerospace industry to see if they can be scaled up to fit into energy-absorbing joints. Shape memory alloys might even help re-centre a building following a quake to reduce repairs. Nickel titanium or Nitinol is one of the earliest materials to exhibit both shape memory and super elasticity. It actually dates to 1959 when it surprised missile designers with its ability to return to its original shape. Concrete containing self-healing capsules can repair cracks. There are even materials that can be made to soften when an electric current is passed through them, so absorbing the energy of an earthquake, then re-stiffened later when the current is removed.
Pre-stressed laminated timber
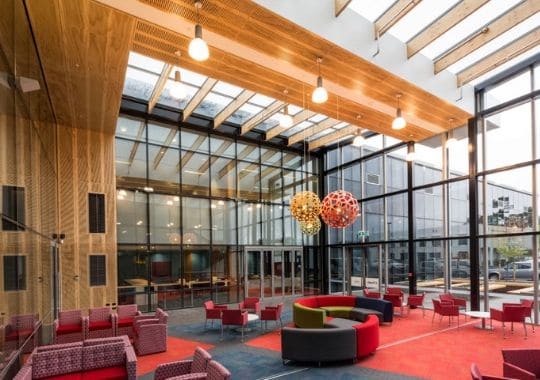
While engineers continue to hunt out exotic new materials that promise seismic defiance, New Zealand’s Trimble Navigation turned to a more familiar technology – wood. After losing its Christchurch offices in a fire following the 2011 earthquake, the company set about looking for a high tech, seismically strong but sustainable replacement. It became the first commercial building in New Zealand to use post-tensioned laminated veneer timber frames and walls. Their natural resilience helps them disperse the energy created during a quake and control the movement of the building itself (which at 6000 m2 became the largest pre-stressed laminated timber building ever constructed). Research at the University of Canterbury helped develop the techniques used by engineering consultancy WSP Opus. The building has since won awards for its innovative use of wood in an engineering project.
High power bracing
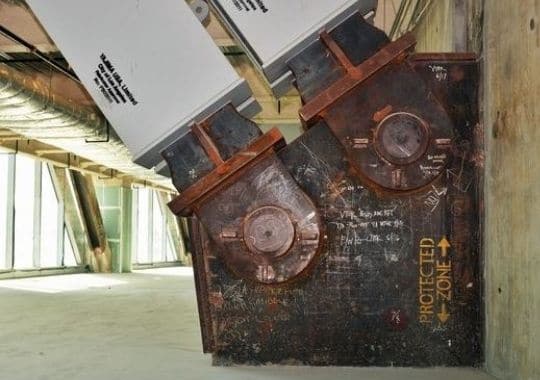
When opened last year, the New Wilshire Grand Centre became the tallest building on the Pacific Coast of America (though at 1,100ft it’s still easily eclipsed by the 1,776ft One World Trade Centre on the far side of the continent). However, California’s propensity for seismic activity made it a tricky project in its own right. Testing the original model against historic data from 11 earthquakes showed the upper levels whipping from side to side at a potentially greater acceleration than a NASA shuttle launch. A key part of the answer was to support the concrete core with a series of outriggers that could reinforce the building. But further tests revealed that the energy being transferred was so substantial it could end
up damaging the concrete itself. So more than 170 buckling-restrained braces were added to yield or stretch and soak up the forces. The use of braces is not new, but the New Wilshire Grand now has the highest capacity system anywhere in the world. Just fitting the top one required loading each brace with 1 million pounds of force. Their dramatic shape has been left exposed as part of the design.
Retrofitting
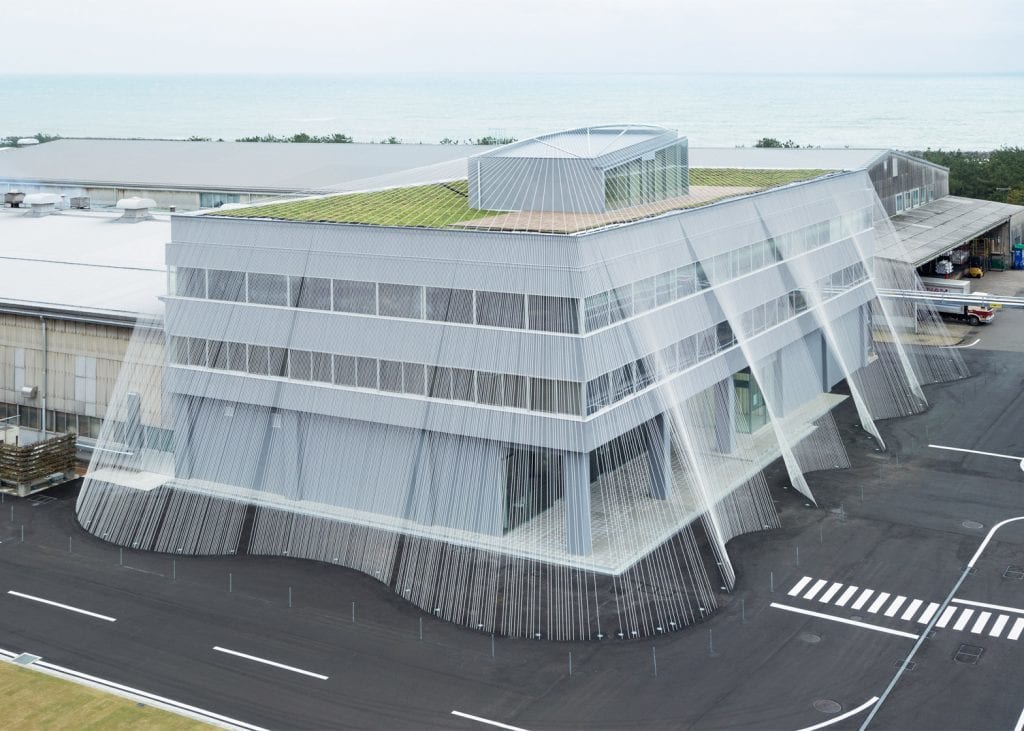
While new buildings can explore the latest earthquake resistant technologies, old buildings need protection too – though retrofitting many of the latest solutions can be all but impossible. One technique that does work is carbon fibre wrapping. Concrete support columns are swathed, sometimes several times, with a mix of carbon fibres and bonding polymers before epoxy is pumped into the gap between the concrete and the wrap. This greatly increasing the columns’ strength. Going one step further, Japanese architect Kengo Kuma retrofitted earthquake resistance into the three storey Komatso Seiren offices in Nomi by wrapping the entire building in the material, creating a carbon fibre curtain around it. It
was Kuma’s statement of how earthquake resistance and aesthetics can combine. In total, 1031 carbon fibres rods are tethered from the roof to the ground (with a further 2,778 inside) to pull the building back into shape when an earthquake moves it.
Why it matters
Between 1994 and 2013, nearly half a million people around the world died due to earthquakes, with another 118.3 million affected. In 2017 scientists predicted an increase in major earthquakes during 2018, brought on by a periodic slowing of the Earth’s rotation. As science and technology expand our knowledge of seismic activity, engineers are concurrently coming up with new and innovative ways to produce earthquake resilient structures.
Keep up to date with news and articles like this one by following Seequent Civil and Environmental on LinkedIn. Or download our Seequent Unearthed report designed specifically for the Civil and Environmental industries. This volume covers topics from sustainability, living and working underground, to where our waste, cars and utilities are going.